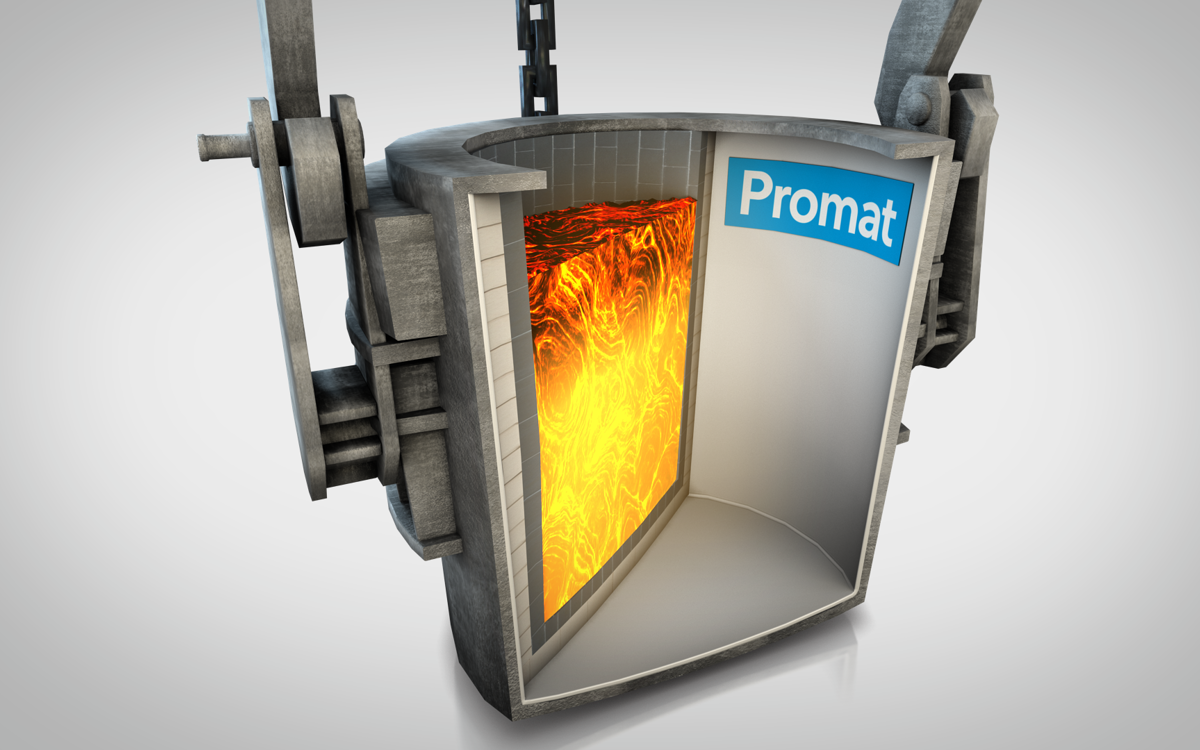
Steel ladles play a crucial role in the steelmaking process, transporting molten steel between different stages of production, but high heat losses in every stage of the production can affect quality and increase energy costs. Promat Microporous insulation have extremely low thermal conductivity, making them highly effective in minimizing heat losses, preventing steel temperature drops, boosting energy efficiency, and extending ladle lifespan by reducing outer shell temperatures. This ensures consistent steel quality and reduces operational costs, enhancing overall production efficiency.
Key Benefits of Promat's Insulation for Steel Ladles
Promat’s Insulation for Steel Ladles delivers exceptional thermal management during the transport of molten steel, forming a protective barrier that preserves high temperatures. By minimizing heat loss, this insulation material provides both immediate and long-term advantages for steel plants. Here’s a closer look at each key benefit:
- Improved Temperature Control: Promat’s insulation effectively maintains stable, high temperatures within the ladle, preventing heat loss and preserving the quality of molten steel during transport. This control ensures that the steel reaches its destination with minimal temperature drop, supporting consistent and high-quality production.
- Extended Ladle Lifespan: The back-up insulation reduces thermal stress on the ladle’s refractory lining, which is critical for protecting against wear and tear caused by extreme temperatures. With less exposure to rapid temperature fluctuations, the ladle’s lining lasts longer, reducing the frequency of maintenance and replacements and lowering overall maintenance costs.
- Energy Efficiency: By minimizing heat loss, Promat’s insulation decreases the need for reheating the molten steel before further processing, conserving energy and reducing operational expenses. This energy efficiency supports both cost savings and sustainable operations, making steel plants more environmentally friendly and economically viable.
With Promat’s insulation for steel ladles, steel plants gain enhanced temperature stability, reduced maintenance needs, and substantial energy savings, contributing to efficient, cost-effective, and high-quality steel production.
Case Study: Insulated vs. Uninsulated Steel Ladles
In a study comparing insulated and uninsulated steel ladles, uninsulated ladles saw significant increases in surface temperatures, leading to faster degradation of the refractory lining and higher maintenance costs. In contrast, insulated ladles maintained lower surface temperatures, extending ladle life, and reducing energy use by up to 15%.
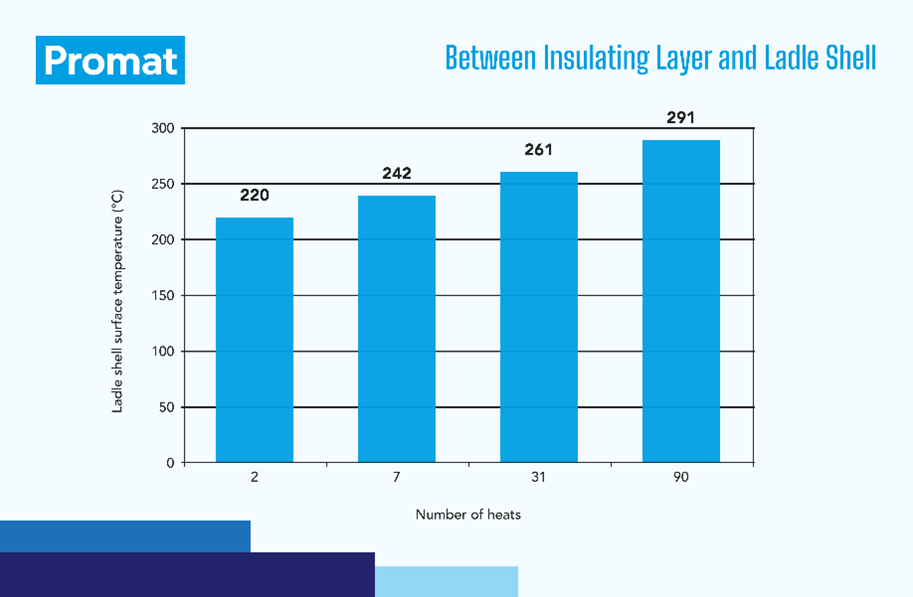

Over the course of a campaign, the ladle shell surface temperature will increase progressively with each heat. However, with Promat’s insulation, the shell temperature remains much lower and more stable versus an uninsulated ladle, even as the number of heats increases.
Figure 2 highlights the effectiveness of Promat’s insulation on ladle shell temperatures. The diagram compares the surface temperatures of insulated versus uninsulated ladles during the steelmaking cycle. The temperature of the ladle shell in uninsulated ladles increases dramatically during each cycle, which places stress on the refractory lining and the external shell, shortening the lifespan of the ladle and increasing safety risks.