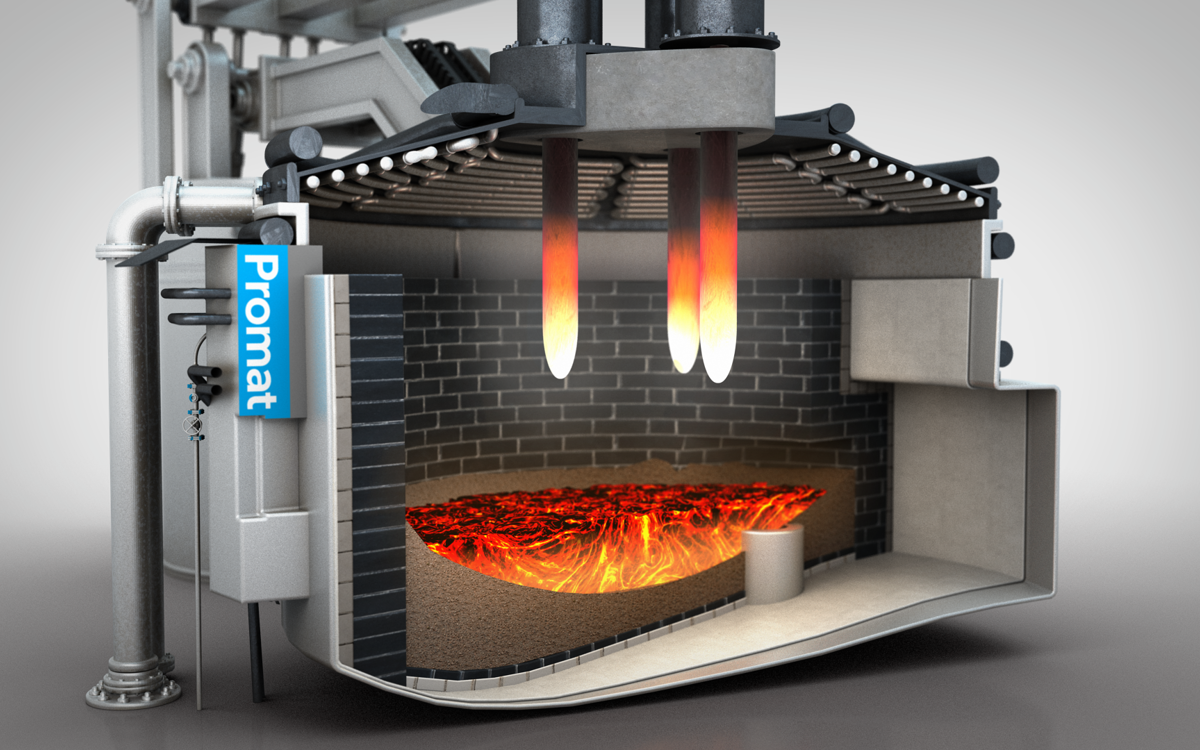
Steelmaking demands advanced thermal insulation to enhance efficiency, cut energy costs, and reduce environmental impact. High-quality insulation minimizes heat loss in processes over 1600°C, optimizing energy use and ensuring reliable output. Promat’s high-performing microporous and vermiculite backup lining materials offer effective solutions for energy savings in extreme temperatures, supporting a more efficient steelmaking process.
In Electric Arc Furnaces, that operates at temperatures reaching up to 1800°C, and therefore consume substantial amounts of electricity, our products can really exel and control heavily heat losses through the walls, avoiding too high operational costs.
Promat’s insulation materials for Electric Arc Furnaces (EAFs), deliver multiple key benefits that optimize the steel production process. Here’s a detailed look at each advantage:
- Enhanced Energy Efficiency: By significantly reducing heat loss, Promat’s insulation solutions ensure that less energy is required to maintain the furnace’s high temperatures. This increased efficiency translates into lower energy consumption overall, making EAF operations more sustainable and cost-effective.
- Reduced Electricity Consumption: With minimized heat escape, EAFs require less electricity to reach and sustain the necessary high temperatures. This reduction in energy demand helps steel plants decrease their electrical costs and reduce the environmental impact associated with high power usage.
- Higher Operating Temperatures: Promat’s insulation materials, like Promalight microporous boards, are engineered to withstand and contain extreme temperatures within the furnace. This capability supports more consistent, high-temperature operations, enabling faster, more efficient processing of materials without frequent shutdowns or temperature fluctuations.
- Extended Electrode Life: By controlling temperature loss, Promat’s insulation reduces strain on the furnace electrodes, which are often exposed to intense heat. This thermal management helps prolong electrode lifespan, minimizing the need for frequent replacements, and further reducing operational costs and downtime.
- Consistent Steel Quality: Stable temperatures within the EAF, achieved through effective insulation, help maintain uniform melting conditions. This stability results in higher quality steel production, with fewer defects and a more consistent end product. The reliable temperature control afforded by Promat’s solutions directly contributes to the production of uniform, defect-free steel.
By integrating Promat’s insulation into EAF operations, steel plants benefit from energy savings, lower maintenance costs, and a higher standard of steel quality, ensuring efficient and reliable production.
Case Study: Heat Loss Reduction in EAFs
Promat’s insulation materials have demonstrated significant improvements in energy efficiency. Studies show that without proper insulation, the shell temperatures of EAFs increase progressively with each heat, leading to higher energy consumption and frequent equipment failures. With Promat’s insulation in place, the shell temperature remains much lower and more stable, even after multiple heats.
For instance, EAFs insulated with Promalight panels showed a 30-40% reduction in energy consumption over time. This reduction was due to minimized heat loss through the furnace walls, allowing operators to maintain optimal temperatures with less electricity. Additionally, electrode life was extended by up to 20%, as the controlled temperature reduced thermal stress on the electrodes.